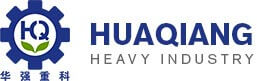
1. Roller part
Wear inspection: Regularly check the wear of the roller surface. Severe wear will affect the granulation accuracy. For example, after long-term use, the pattern on the roller surface may be worn flat, resulting in poor granulation. If the wear exceeds the specified range, the roller needs to be replaced in time.
Gap adjustment: Accurately adjusting the roller gap is the key. Different materials and granulation requirements correspond to different gaps. If the gap is too small, the roller extrusion resistance is too large, which increases the equipment load; if the gap is too large, the granulation effect is poor. According to production requirements, use professional tools for precise adjustment.
2. Transmission parts
Belt or chain maintenance: Check the tightness of the belt or chain. If it is too loose, it is easy to slip, making the roller speed unstable; if it is too tight, it will accelerate wear and shorten the service life.
Bearing maintenance: lubricate and check the bearings of the Double Roller Press Granulator regularly. If the bearings are lacking in oil, abnormal friction will occur, causing the temperature to rise and affecting the normal operation of the equipment. At the same time, check whether the bearings are loose or damaged.
3. Material supply system
Feed uniformity: Ensure that the feed is uniform and stable. Uneven feed will cause uneven force on the rollers, affecting the continuity and quality of granulation. A flow regulating device can be installed to ensure that the material enters the rollers evenly.
Feed port cleanliness: Keep the feed port clean to prevent material agglomeration from blocking the feed port. Blockage will cause the rollers to run idle or some materials cannot be granulated normally.
4. Overall equipment inspection
Structural stability: Check the frame, bracket and other structural components of the equipment to see if the bolts are loose. Loose bolts may cause the equipment to vibrate during operation, affecting the granulation effect and equipment life.
Cleaning and anti-corrosion: Clean the surface of the equipment regularly to remove dust, material residues, etc. For parts that are prone to corrosion, anti-corrosion measures should be taken, such as applying anti-rust paint.
The above are the daily maintenance measures for the Double Roller Press Granulator. Of course, in the actual production process, some unexpected situations are inevitable. We must solve them in time according to the actual situation to ensure the efficient operation of the Double Roller Press Granulator.