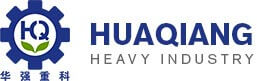
The disc granulator of Zhengzhou Huaqiang Heavy Industry Machinery Co., Ltd. has the following advantages: high spheroidizing rate, high roundness and strength of particles, intuitive operation, convenient maintenance, etc.
The working principle of the disc granulator machine for fertilizer: pre-adding water to form a ball-disc full-disc pelletizing method. The raw meal powder is evenly moistened by the atomized water in the double-shaft mixer to form a ball core with a very uniform particle size, and then sent to the ball-forming plate for ball formation. The water content of the pellets should be controlled at 12-14%. Most of the water should be added in the double-shaft mixer, and only a small amount of supplemental water should be added to the ball pan, and the supplemental water amount should be controlled at about 0-3%. The dry powder granulation is directly added to the ball-forming disc, and an appropriate amount of water is sprayed. After the raw material ball core enters the ball-forming disc, it moves along the parabola under the action of centrifugal force, friction and gravity in the disc. Due to the cohesiveness and plasticity of the material, the cores adhere to each other during the movement and gradually grow up. When the inclination angle of the ball, the height of the disc, the rotation speed and the moisture content are constant, the balls of different particle sizes will leave the disc edge and roll down at different detachment angles due to different gravity. The material ball continuously pushes the water out of the surface during the continuous rolling process. Due to the cohesiveness of the material and the natural volatilization of the surface liquid film, the material ball has certain strength, and then follows the rotation of the inclined plate body. The edges are discharged out of the tray.
Stirring tooth fertilizer granulator machine:
The new type of organic fertilizer granulator is also called a spiral stirring tooth structure because of its internal structure. It uses the high-speed rotating mechanical stirring force and the resulting aerodynamic force to continuously mix the fine powder in the machine. The process of granulation, spheroidization, and densification, so as to achieve the purpose of granulation. The particle shape is spherical, the sphericity is 0. The particle size is generally between 0.3-3 mm, and the granulation rate is 90%. The particle diameter can be appropriately adjusted by the mixing amount of the material and the spindle speed. Generally, the lower the mixing amount, the higher the rotation speed. Higher, the smaller the particles, and vice versa. Application range: This machine is especially suitable for the granulation of light and fine powder materials. The finer the basic particles of the fine powder material, the higher the sphericity of the particles, and the better the quality of the pellets. It is generally required that the particle size of the material before granulation should be less than 200 mesh. Typical application materials: chicken manure, pig manure, cow manure, carbon black, clay, kaolin, etc. It is specially used for granulation of urban domestic waste organic fermented fertilizer such as organic fertilizer raw materials, livestock and poultry manure, compost fertilizer, green manure, sea manure, cake fertilizer, grass charcoal, soil and miscellaneous fertilizer, three wastes, microorganisms, etc. The particles are spherulites. The machine adapts to a variety of different formulas. The compressive strength of organic fertilizer is higher than that of discs and drums, and the ball rate is lower than 15%. The uniformity of particle size can be adjusted by the stepless speed regulation function of this machine according to user requirements. This machine is most suitable for the direct granulation of organic fertilizer after fermentation, which saves the drying process and greatly reduces the manufacturing cost.