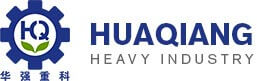
1) Nitrogen fertilizers: ammonium chloride, ammonium sulfate, ammonium sulfate, urea, calcium nitrate, etc.
2) Potash fertilizers: potassium sulfate, plant ash, etc.
3) Phosphate fertilizers: superphosphate, superphosphate, calcium magnesium phosphate, phosphate rock powder, etc.
The extruded organic fertilizer granulator machine should prevent the granulated powder material from being in the extrusion granulation equipment, and then use external force to compact the powder material tightly. Due to the different external force methods used, the molecules are recombined to make the material appear as cylindrical particles. The whole process of generation and extrusion is mechanized operation, no manual operation is required. Stirring and granulation mainly use the method of stirring to shape the material into a round shape.
Advantages of the roll extrusion fertilizer granulator machine:
The extrusion granulation method requires less equipment and less investment. The results of a study conducted by the International Fertilizer Development Center (NFDC) in developing countries in 1987 showed that:
1. For the annual output of 10,000-100,000 tons of granular N, P, K fertilizer equipment, the investment in extrusion granulation is only 50% of slurry granulation or chemical granulation, which is 20 less than steam granulation;
2. Extrusion granulation does not require heating and humidification of materials, saving investment and energy consumption, and can be adapted to the granulation of ingredients containing heat-sensitive materials, such as ammonium bicarbonate and certain organic substances;
3. No waste water or waste gas is discharged outside during the production process, and it will not pollute the environment;
4. The extrusion granulation process is short, easy to operate, easy to realize automatic production control, and improve production efficiency;
5. There are no special requirements on the nature and particle size distribution of the raw materials, so the source of raw materials is wider, and the production is more flexible. If the product plan needs to be changed, it is more convenient and beneficial to the production of special fertilizers in small batches;
6. The product has uniform particle size distribution, high hardness, no segregation, and no agglomeration.
The large flakes produced by the extruded organic fertilizer granulator equipment have a thickness of 5-20mm and a surface density of 1.5-3 times that of the feed. The large flakes are then flakes, crushed and sieved to obtain the required granular products. The particles formed by pressure will form a hot spot on the contact point to melt the material. After the temperature drops, the material cools to form a fixed bridge. The above is a detailed introduction of the granulation method of the organic fertilizer granulator. You can learn more about it. There are many methods of organic fertilizer granulation. The extrusion granulation method can be said to be a commonly used one, so we have to deal with this the method is more skilled, so as to ensure the quality of the granulation of the organic fertilizer granulator.