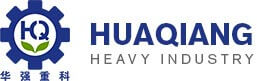
1. If the granulation rate reaches more than 90%, and the same specification is not completed, it can also enter the machine again for secondary processing.
2.The cylinder can be rotated with less power, and the exterior is made of wear-resistant steel, which effectively prolongs the use time of the equipment.
3. It is a special molding machine that can be made by rolling materials through chemical reactions. Under the action of a certain liquid, the rolling of the cylinder is used to squeeze the materials and small particles into a sphere.
4. The most energy-saving supporting roller bracket is used for support. The bracket is made of high-quality carbon steel, which can fully bear the weight of the cylinder. Considering the large friction between the cylinder and the supporting wheel, in this part deliberately using more wear-resistant materials, on the one hand, it can improve the safety of the equipment and also improve the stability.
5. The transmission device is an important part that provides the main movement of the machine. The gear ring on the cylinder is driven by the motor and reducer on the shelf. The shelf is welded with professional and non-deformable high-quality channel steel to make the machine drive The device is more secure and stable.
The reducer of the fertilizer granulator machine drives the belt through the motor. There is a pinion on the shaft of the reducer, which coincides with the teeth on the ring gear outside the fuselage. The cylinder and the reducer move in opposite directions, and the material is moved from the silo or conveyor. The material is sent to the end of the barrel, and the material is made into small granular materials in the barrel, and the material that meets the finished product is discharged from the discharge port at the other end. Through the continuous operation of the machine, large-volume production can be realized.
Installation and debugging of the roller granulator:
1. Installation: After the roller extrusion granulator arrives at the factory, the granulator is used as the main machine. It depends on the number of units and is installed in conjunction with the granulation process flow chart. Find out the elevation and horizontal placement. The machine frame, there are ground corner holes, which can be installed on concrete.
2. Debugging: The machine has been debugged before leaving the factory, and it still needs to be debugged after trial.
(1) Press roller gap adjustment: Sometimes it is necessary to increase the output or increase the bite angle during production. At this time, the distance between the two shafts can be increased, and the distance between the driving shaft roller and the driven shaft can be increased.
(2) The alignment adjustment of the ball and socket
The ball socket is formed by the indentation of the concave sockets on the surface of the main roller, so there is the problem of axial alignment and circumferential alignment.