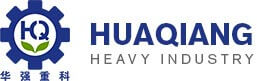
1. Raw material processing
Particle size control: The raw material particle size should be moderate and uniform. Too coarse raw materials are not easy to stick into balls, and too fine may cause the pellet structure to be loose. Therefore, the raw materials need to be strictly crushed, screened and measured to ensure the quality of the materials.
Humidity adjustment: The humidity of the raw materials is a key factor. If the humidity is too high, the material is easy to form large lumps in the disc; if the humidity is too low, it is difficult to form round particles. Therefore, the humidity needs to be adjusted according to the characteristics of the raw materials, generally kept at 10% - 20%.
2. Adjustment of disc parameters
Tilt angle: The appropriate tilt helps the material to roll out smoothly. If the tilt is too large, the material will be discharged too quickly and the ball formation will be incomplete; if the tilt is too small, the material will easily accumulate in the disc. Usually the tilt can be set between 45 and 60 degrees.
Speed adjustment: The speed of the disc is also a key factor affecting the efficiency and quality of ball formation. If the speed is too fast, the material will roll too violently in the disc and cannot be effectively gathered into balls; if the speed is too slow, the production efficiency will be low. Therefore, the appropriate speed can ensure the uniform distribution and effective rolling of the material in the disc, thereby improving the ball formation rate and particle quality.
3. Use of binder
Choose a suitable binder according to the characteristics of the material to improve the adhesion of the material. At the same time, the position of spraying the binder into the disc should be correct, and the binder should be in a mist state when sprayed out so as to better mix with the material.
4. Operation precautions
Stable feeding: Maintain a uniform and stable feeding speed to avoid the feed amount being too much or too little. When the feed amount is too little, large particles may appear; when the feed amount is too much, the rolling time of the material in the disc will be shortened, resulting in the formation of particles that are too small. Therefore, stable feeding can ensure the stability of the amount and state of the material in the disc, which is conducive to continuous and efficient granulation.
Regular maintenance: Regularly clean the residual materials, adhesives and other impurities in the disc, check the wear of the disc, and replace the worn parts in time to ensure the normal operation of the equipment.
In actual production, it is necessary to pay close attention to the operating status and product quality of the Disc Granulator, and make timely adjustments and optimizations to ensure the stable improvement of the balling efficiency, thereby improving production efficiency.