The process principle of
Double Roller Press granulator
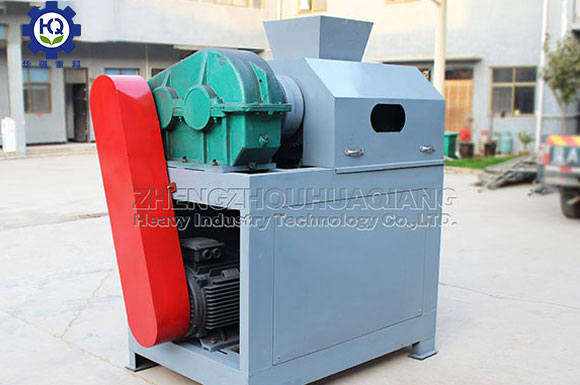
The dry material is aggregated into dense and hard chunks (cake) under the action of pressure, which is called the extrusion process; The cake material is then broken by the
cage crusher and screened by the
drum screener machine to become granular material called granulation process. The effect of extrusion is to push out the air between the particles, and to make the particles close enough to produce attractive forces such as van der Waals forces, adsorption forces, crystal Bridges, and embedded connections. The particle strength of extruded granulation is mainly formed by the force between molecules.
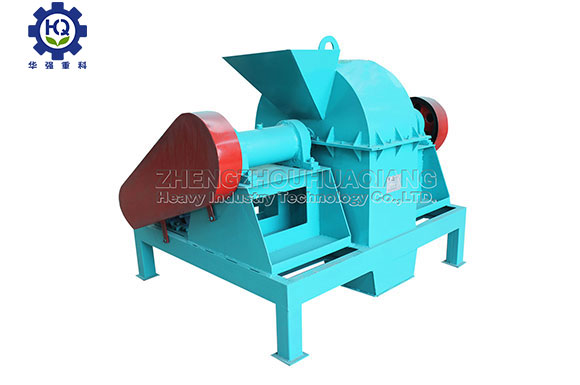
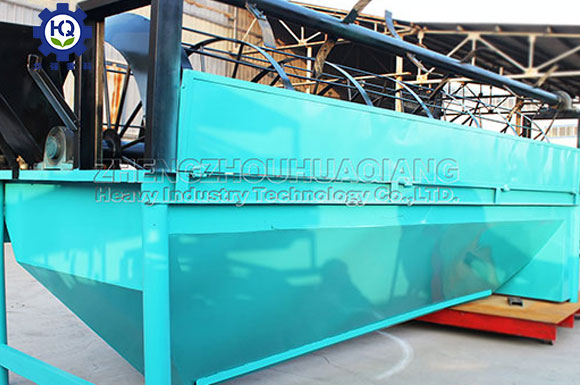
Advantages of extruded granulation:
1) Energy saving extrusion granulation is the material granulation at room temperature, compared with other methods, do not need fuel, gas and other drying measures.
2) There is no need to add additional adhesive. The commonly used compound fertilizer production method (
new type stirring tooth-drum granulator) in China is steam granulation. After the water vapor condenses and crystallizes between the molecules of the material, it acts as an adhesive during the manufacturing process. However, in the drying process, the water inside and on the surface of the particles must be driven out, otherwise the fertilizer is easy to bond and caking during storage. The dry granulation method does not require additional additives, and only needs to use the intermolecular force of the material itself, which simplifies the process and reduces energy consumption.
3) Low investment Due to the elimination of the drying process, while the material return ratio is low (accounting for about 15% of the total feed volume of the extruder), the process is simple and the investment is low.
4) Raw material composition Flexible extrusion granulation production raw material route is more extensive, has been successfully used for extrusion granulation of more than 20 kinds of materials: ammonium nitrate, urea, ammonium chloride, calcium nitrate, potassium chloride, potassium sulfate and so on. In addition, the use of extrusion granulation process can flexibly achieve the replacement of product formulations in a very short time, and a set of devices can produce more than 30 formulations of products.
5) Green environmental protection without three waste emissions, extrusion granulation consumption capacity, only for electricity, environmental protection without three waste emissions, to adapt to the basic national policy on environmental protection, but also in line with the development strategy of enterprise environmental protection.