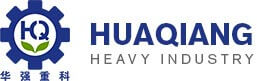
1. Cleaning work: After each use, thoroughly remove the residue inside and outside the equipment, especially the dust prone parts such as the hopper and stirring blades. Keep the outer surface of the equipment clean to prevent corrosion and clogging.
2. Lubrication maintenance: According to the requirements of the equipment manual, choose the appropriate lubricating oil or grease for regular lubrication. Bearings, chains, gears and other transmission components are regularly lubricated to reduce friction and wear. Pay attention to the amount of lubricating oil added to avoid excessive lubrication caused by waste and pollution.
3. Routine inspection: appearance check whether the equipment is worn, deformed or cracked; Connecting parts Check whether the device is securely connected; Run sound check, pay attention to whether there is abnormal sound when the equipment is running, such as metal friction sound or abnormal response immediately stop the check.
4. Safety device inspection: Regularly check the safety device of the equipment, such as protective cover, safety switch, etc., to ensure that it is sensitive and reliable to prevent accidents.
5. Storage and protection: When the equipment is not used for a long time, it should be stored in a dry, ventilated and dust-free place to avoid moisture or damage to the equipment. For exposed processing surfaces and equipment components, cover them with a shield or dust cloth to prevent the intrusion of dust and debris.
6. Maintenance and maintenance records: Establish maintenance and maintenance records of the equipment, record the time, content and results of each maintenance and maintenance, so as to facilitate future management and maintenance.
7. Organic Fertilizer Production Line: The maintenance of the production line is the key to ensure production efficiency. Regularly check all aspects of the production line to ensure the normal operation of the equipment, timely replacement of worn parts, and maintain the flow of the production line.
8. Fertilizer granulator series: For granulators, such as Fertilizer Granules Compaction Machine and Flat-Die Pellet Machine, special attention should be paid to the wear of the mold, and the mold should be replaced regularly to ensure the quality of granulation.
9. Compost tiller: Tiller maintenance should pay attention to check whether the tiller knife defect and fastening bolts are loose, if necessary, complete, tighten or replace a new knife.
10. Fertilizer Crusher: For the crusher, such as Cage Crusher, it is necessary to regularly check the wear of the hammer and replace it in time to ensure the crushing effect.
11. Fertilizer mixer: The maintenance of the mixer should pay attention to the accuracy and balance of the transmission components, and regularly adjust the mixing blade to ensure that the mixing is uniform.
12. Fertilizer screening machine: the screen of the screening machine should be regularly checked for wear and timely replacement to ensure screening efficiency.
13. Fertilizer drying and cooling machine machinery: the maintenance of the dryer and cooling machine should pay attention to the cleaning of the heat exchanger, regularly clean the dust, and ensure the heat exchange efficiency.
14. Other supporting equipment: such as Uniform Feeder, it is necessary to check the uniformity and accuracy of feeding regularly, adjust the feeding speed, and ensure the continuity and uniformity of feeding.
Through the above measures, the organic fertilizer equipment can be effectively maintained and maintained, the use efficiency and life of the equipment can be improved, and the product quality of organic fertilizer can be ensured.